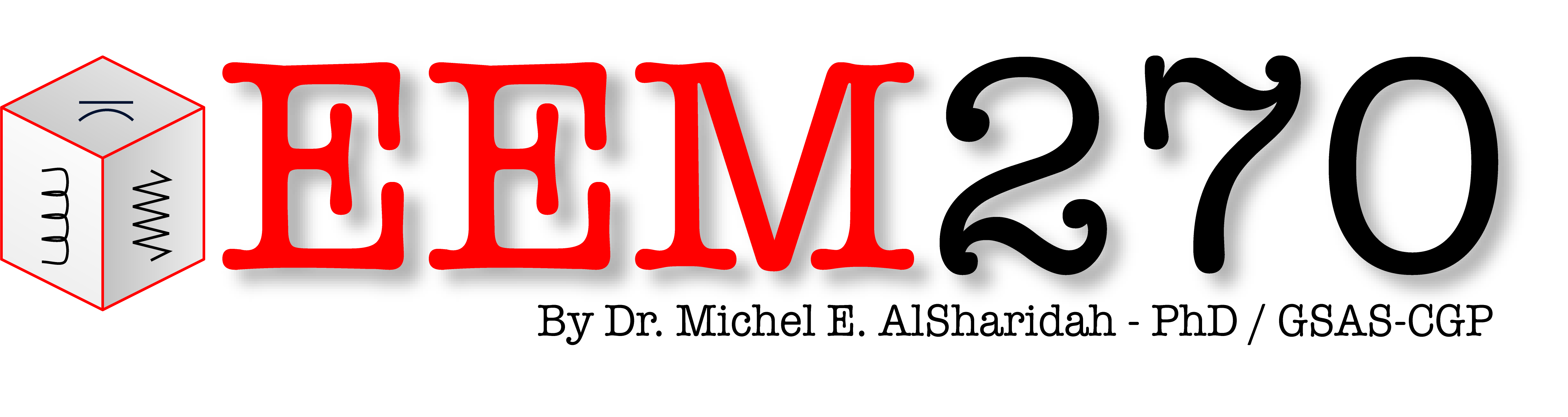
CTSEET is the documentation website for courses offered by Dr. M. E. AlSharidah. It records all course descriptions, learning outcomes, objectives, syllabus, and notes.
CTSEET is the documentation website for courses offered by Dr. M. E. AlSharidah. It records all course descriptions, learning outcomes, objectives, syllabus, and notes.
This course describes the principle of electrical drive systems, their types, elements, characteristics, performance parameters, and applications. Single-phase dc drive systems - Three-phase dc drive - Three-phase induction motors drive systems. DC chopper drive systems - Braking system; dynamic braking, and regenerative braking. Introduction to UPS systems; types, characteristics, performance parameters, specifications, and applications. High frequency link UPS systems - Static bypass - Monitoring parameters. Batteries; types, characteristics, specifications, troubleshooting, and applications. Battery chargers; types and performance.
% | Category | Notes |
---|---|---|
10 | Atendance/Activity | 2.5% will be deducted for every 4hrs absense |
40 | HW/Simulation | Lab reports is based on MATLAB/Simulink R2018+ simulation |
20 | Midterm | 6-8 problem type questions |
30 | Final Exam | 8-10 problem type questions |
Event | Date |
---|---|
Course starts | Sun 2024-09-16 |
Last day of classes | Thu 2024-12-19 |
Course ends | Tue 2025-01-09 |
Lab | Date | Experiment |
---|---|---|
1 | 2024-10-14 | Modeling and Speed Control of Separately Excited DC Motor |
2 | 2024-10-28 | Single-phase SCR DC drive |
3 | 2024-11-19 | Speed control of DC Motor using SP-FC-FWR |
4 | 2024-11-25 | Control of DC machine using DC to DC converter |
The following is a list of per-lecture expected performace criteria and learning objectives. The Student should use this guide to assess his progress in the course.
Recognize the structure of Electric Drive systems and their role in various applications
Describe the basic characteristics of DC motors and their control parameters
Recognize the various types of DC motor drives
Explain a single-phase SCR DC Drive
Explain Three-Phase DC Drives
a. Describe three phase half-wave converter drives.
b. Describe three phase full-wave converter drives.
c. Analyze three-phase full- and half-wave rectifier control of DC drives.
d. Analyze three-phase rectifier fed separately excited DC motor.
e. Study of torque-speed characteristics of three-phase controlled converter drive.
f. Utilize manufacturer manuals to connect a three-phase DC Drive to operate a DC motor.
g. Measure electrical quantities and waveforms to determine correct DC drive operation.
h. Work in teams to perform laboratory experiments.
i. Simulate a three-phase controlled DC drive.
Explain DC-DC Converter Drives
Explain the various methods of three-phase induction motor drives
Explain Adjustable Frequency Drives (AFDs)
Explain Uninterruptible Power Supply (UPS)
Study storage batteries and battery charging
The following selected chapters give in depth explanation on subjects related to the course.
Title | MATLAB instructional videos – MATLAB فيديوهات تعليمية ل | العنوان |
---|---|---|
Introduction to Matlab | مقدمة MATLAB | |
Math operations | العمليات الرياضية | |
Logic operation | العمليات المنطقية | |
Matrices | المصفوفات | |
Plots | الرسومات | |
Introduction to Simulink | مقدمة Simulink | |
Using Simulink | استخدام Simulink | |
Electric circuits in Simulink | الدوائر الكهربية في Simulink | |
Circuit example | مثال لدائرة كهربية | |
DC motor speed control | التحكم في سرعة آلة التيار المستمر |
All course lecture and labs recorded meetings and notes
$P=T \cdot \omega_m$
if $P < 0$ power flow from M to PS
I : $T \gt 0$ & $\omega_m \gt 0$ $\longleftrightarrow$ forward motoring
II : $ T \lt 0 $ & $\omega_m \gt 0$ $\longleftrightarrow$ forward breaking
III: $T \lt 0$ & $\omega_m \lt 0$ $\longleftrightarrow$ reverse motoring
IV: $T \gt 0$ & $\omega_m \lt 0$ $\longleftrightarrow$ reverse breaking
$$\begin{equation} T_L = T_F + T_L^*\end{equation}$$
where $ T_L^*$ is the physical load torque and $T_F$ is the motor friction torque.
The friction torque \eqref{TF} is composed of a number of motor related frictions. Some are constant, some are short lived, and others related to speed.
$$\begin{equation}T_F = T_S + T_C + T_V + T_W\label{TF}\end{equation}$$
During steady-state operation, The motor drives a load and speed will not vary at this stage. Constant speed means that there is no acceleration and $\frac{d\omega_m}{dt}=0$. Therefore:
$$T = J \frac{d \omega_m}{dt} + T_L $$
and hence, $T=T_L$, assuming the torque due to friction is zero for simplicity or that the load torque contains the useful load and friction values. To find out the operating point (Q), the operating point is defined by the intersection of the motor characteristic with the load characteristics. It means the motor will be running at the speed and the corresponding torque will be as shown in the figure below.
The condition for stable operation is $\frac{dT_L}{d\omega_m} \gt \frac{dT}{d\omega_m}$. Below is mathematical stability analysis proofing this condition.
$$T = T_L + J \frac{d\omega_m}{dt} \tag{a}\label{eq:a}$$
now in order to find out if the operting point Q in the figure above is stable, we perturb the torque by $\Delta T$ and monitor speed behaviour in small signal analysis sense.
$$\begin{align} T + \Delta T &= T_L + \Delta T_L + J \frac{d}{dt}(\omega_m + \Delta \omega_m) \tag{b}\label{eq:b}\\
\Delta T &= \Delta T_L + J \frac{d}{dt} \Delta \omega_m \tag{c} \label{eq:c}
\end{align}$$
Taking \eqref{eq:b} minus \eqref{eq:a} results in the small signal equation \eqref{eq:c}. Here we define of $\Delta T$ and $\Delta T_L$ are as follows:
$$\begin{align}\Delta T = \frac{dT}{d\omega_m} \cdot \Delta \omega_m \tag{d}\label{eq:d}\\
\Delta T_L = \frac{dT_L}{d\omega_m} \cdot \Delta \omega_m\tag{e}\label{eq:e}
\end{align}$$
substitution of \eqref{eq:d} and \eqref{eq:e} in \eqref{eq:c} yeilds
$$ \frac{dT}{d\omega_m} \cdot \Delta \omega_m = \frac{dT_L}{d\omega_m} \cdot \Delta \omega_m + J \frac{d}{dt} \Delta \omega_m \tag{f}\label{eq:f}$$
rearranging \eqref{eq:f} and solving for $\Delta \omega_m$
$$\begin{align}0 &= J \frac{d}{dt} \Delta \omega_m + \left [ \frac{dT}{d\omega_m} - \frac{dT_L}{d\omega_m} \right ] \tag{g}\label{eq:g}\\&\nonumber\\
\Delta\omega_m & = \Delta \skew{2}{\hat}\omega_m \cdot e^{-\frac{1}{J} \cdot \left [ \frac{dT}{d\omega_m} - \frac{dT_L}{d\omega_m} \right ]}\tag{h}\label{eq:h}\end{align}$$
where $\Delta\skew{2}{\hat}{\omega}_m$ is the initial condition of the motor speed.
$\Rightarrow$ if $t \rightarrow \infty$ then $\Delta\omega_m \rightarrow 0$ and accordingly $\left [ \frac{dT}{d\omega_m} - \frac{dT_L}{d\omega_m} \right ] \gt 0$ and the condition for steady-state is satisfied by \eqref{eq:i}
$$ \frac{dT_L}{d\omega_m} \gt \frac{dT}{d\omega_m} \tag{i}\label{eq:i}$$
$$V=E+I_a R_a\tag{1}$$
$$I_a=\frac{V-E}{R_a}\tag{2} \gt 0$$
$$E=V-I_a R_a\tag{3}$$
$$\omega_m=\frac{V}{K\phi}-\frac{T R_a}{(K\phi)^2}\tag{4}$$
Condition:
$$V=E+I_a R_a\tag{5}$$
$$I_a=-\frac{E-V}{R_a} \lt 0\tag{6}$$
$$E=V-I_a R_a\tag{7}$$
$$\omega_m=\frac{V}{K\phi}-\frac{T R_a}{(K\phi)^2}\tag{8}$$
Condition:
$$0=E+I_a R_a\tag{9}$$
$$I_a=-\frac{E}{R_a}\lt 0\tag{10}$$
$$E=-I_a R_a\tag{3}$$
$$\omega_m=-\frac{T R_a}{(K\phi)^2}\tag{11}$$
Condition:
$$V=-E-I_a R_a\tag{12}$$
$$I_a=-\frac{V+E}{R_a}\tag{13}\label{eq13}$$
$$E=-V-I_a R_a\tag{14}$$
$$\omega_m=-\frac{V}{K\phi}-\frac{T R_a}{(K\phi)^2}\tag{15}$$
Condition:
Matlab v2018a or above is required to run this file. Click the link below to download the file.
Write, in your own words (arabic or english) about the experience and challenges during this lab experiment. Highlight the strog concepts aquired and mention any weaknesses. Suggest any improvement.
Matlab v2018a or above is required to run this file. Click the link below to download the file.
Verify the mesured back EMF value by using the back EMF equation
$$E=\frac{V_{m}(\cos \alpha-\cos B)}{(\beta-\alpha)} -\frac{R_a I_a}{(\beta-\alpha)} $$
Using the equation below, verify that the value of $\beta$ satisfies the equality. If there is discrepancy, adjust $\beta$ so that the equation is satisfied within 0.1% error margin.
$$ 0=\frac{V_m}{Z} \sin (\beta-\theta)-\frac{E}{R_a}+\left[\frac{E}{R_a}-\frac{V_m}{Z} \sin (\beta-\theta)\right]\cdot e^{-(\beta-\alpha)\cot(\theta)} $$
$$ \omega_m=\frac{V_m(\cos \alpha-\cos \beta)}{k \phi(\beta-\alpha)}-\frac{T \cdot R_a\cdot \pi}{(K \phi)^{2}(\beta-\alpha)} $$
Write, in your own words (arabic or english) about the experience and challenges during this lab experiment. Highlight the strog concepts aquired and mention any weaknesses. Suggest any improvement.
Matlab v2018a or above is required to run this file. Click the link below to download the file.
عند تنزيل الملف تاكد من ان يكون اسم الملف خالي من الفراغات و الاقواس وعلامة الناقص
Ensure to save the Lab 3 folder in the MATLAB folder and verify that the name of the folder does not contain invalid characters.
In this experiment, the speed of the DC-motor is controlled by using an open-loop voltage control via firing angle $\alpha$ of the SCR based SP-FC-FWR and a closed loop speed control via speed and current PI control. The purpose of this experiment is to implement a close-loop speed control of a DC-motor drive. The standard 5HP DC-motor is used where its parameters are given in the motor block of the experiment. The controller will be tested on a simulation model of the DC-motor.
1) Explain two advantages of the Electric Drive System of the Electric motors?
2) A very important power electronic device is the Silicon Controlled Rectifier "SCR". Explain the construction, the function and the characteristics of the device.
Run the simulation (with default configuration parameters) for the following two cases. Compare the observed values with calculated values. Save the plots and include them in your report.
Time=[0 3 6 9 12 15 18 21 24 27 30 33 36 39 42 45];
TL=[2 4 6 8 10 12 14 16 18 20 22 24 26 28 30 32];
Time=[0 3 6 9 12 15 18 21 24 27 30 33 36 39 42 45];
TL=[2 4 6 8 10 12 14 16 18 20 22 24 26 28 30 32];
SPEED=100*[1 1 1 1 1 1 1 1 1 1 1 1 1 1 1 1];
Change the reference speed to 800RPM by myliplying the speed vector by 8 as in
SPEED=SPEED*8;
Observe and compare the speed and torque ripple for both cases (100 rpm and 800 rpm), give an explanation for the differences.
In yout own words, write the advantages and benefits for adapting a speed controller. What are the limitations when implementing a SP-FC-FWR for DC motor speed control?
Matlab v2018a or above is required to run this file. Click the link below to download the file.
عند تنزيل الملف تاكد من ان يكون اسم الملف خالي من الفراغات و الاقواس وعلامة الناقص
Ensure to save the Lab 4 folder in the MATLAB folder and verify that the name of the folder does not contain invalid characters.
In Lab 3 experiment, motor speed control was achieved via a single-phase fully-controlled thyristor-based fullwave rectifier and speed control was demonstrated. In this Lab, the objectives are:
1) Observe the four-quadrant speed operation of a DC motor.
2) Control the speed of the DC motor and observe the effect of a stepped torque.
1) Save the waveform for the speed, torque, armature current and armature voltage label the quadrant of operation. [D_ref: 0.3, 0.6, 0.9; Torque: 20 N.m, -20 N.m]
2) Give a step change in load torque from 0 to 20 N.m (TL) at t = 1 s and note the resultant speed for each D_ref setting. Elaborate on the effect of changing D_ref.
3) Theoretically estimate the no-load speed value in rpm for each case
4) What is the net power supplied by the motor? What is the quadrant of operation for all the scenarios?
1) Save the waveform for the speed, reference speed, torque, armature current and armature voltage label the quadrant of operation.
2) Give a step change in load torque from 0 to 20 N.m (TL) at t = 1 s and note the resultant speed.
3) Theoretically estimate the no-load speed value in rpm.
4) What is the net power supplied by the motor? What is the quadrant of operation?
5) repeat tasks 1-4 for all of the combinations of step torque and reference speed. [speed: 1000 rpm, -1000 rpm; Torque: 20 N.m, -20 N.m]
Describe the advantages of this method of speed control.
In yout own words, write the advantages and benefits for adapting this speed controller. What are the limitations, if any, when implementing a four quadrant DC chopper for DC motor speed control?
This chapter includes practice questions and problems that will assist in preparing for the midterm exam. Each set is of questions addresses material covered in the lectures, respectively. (i.e. set 1 $\rightarrow$ lecture 1)
a. Armature resistance control
b. Armature voltage control
c. Field resistance control
d. Diverter resistance control in field circuit
a. Load
b. Sensing Unit
c. Power Modulator
d. Mechanical Gear
a. AC voltage regulator
b. Cycloconverter
c. Fully controlled converter
d. Half controlled converter
where $J$ is moment of inertia in $kg\cdot m^2$, B is the coefficient of viscous friction in $N\cdot m$/(rad/s) and $\omega_m$ is the rotor speed in rad/sec.
a. $J\cdot \dfrac{d\omega_m}{dt}$
b. $J\cdot \dfrac{d^2\omega_m}{dt^2}$
c. $B\cdot \omega_m$
d. $B\cdot \omega_m^2$
a. 0.54 $kg\cdot m^2$
b. 0.64 $kg\cdot m^2$
c. 0.74 $kg\cdot m^2$
d. 0.84 $kg\cdot m^2$
a. 3873 Watt
b. 4873 Watt
c. 5873 Watt
d. 6873 Watt
a. Fan type of load
b. Traction load
c. Low speed hoist load
d. Constant power load
a. Coulomb friction
b. Static friction
c. Viscous friction
d. Windage friction
a. Traction load
b. Low speed hoist
c. Fan type of load
d. High speed hoist
$T = 100 - 0.1 \omega_m$ ($N\cdot m$)
$T_L = 0.05\cdot \omega_m$ ($N\cdot m$)
where T = motor torque in $N\cdot m$, $T_L$ = load torque in $N\cdot m$ and $\omega_m$ = speed of the motor-load combination in rpm. The steady state speed of the drive is:
a. 333.33 rpm
b. 455.55 rpm
c. 666.66 rpm
d. 721.66 rpm
Motor: $T=1+2\cdot \omega_m$
Load: $T_L=3\cdot \sqrt{\omega_m}$
The steady state equilibrium speeds are:
a. $1$ & $1/4$
b. $1$ & $1/2$
c. $2$ & $1/4$
d. $2$ & $1/2$
a. $2$
b. $3/2$
c. $1$
d. $1/4$
a. By connecting an inductance in series with the motor.
b. By connecting a flywheel with the motor-load combination.
c. By controlling the triggering angle of the converter feeding the motor.
d. By introducing a gear with appropriate gear ratio.
a. 50.0 $N\cdot m$
b. 45.2 $N\cdot m$
c. 35.2 $N\cdot m$
d. 25.2 $N\cdot m$
a. 100 rad/s
b. 64.7 rad/s
c. 356.9 rad/s
d. 37.7 rad/s
a. Armature resistance control
b. Armature voltage control
c. Field resistance control
d. Controlling resistance in parallel with armature
a. $V/(K\phi)$
b. $V/(K\phi)^2$
c. Zero
d. In finite
a. 1115 rpm
b. 1222 rpm
c. 1328 rpm
d. 1404 rpm
a. $30^o$
b. $45^o$
c. $60^o$
d. $75^o$
a. 149V
b. 169V
c. 179V
d. 189V
a. 179 rad/s
b. 169 rad/s
c. 159 rad/s
d. 129 rad/s
a. Higher than the critical speed
b. Lower than the critical speed
c. Higher than 50% of the critical speed
d. Lower than 50% of the critical speed
a. A closed form solution of the relevant equation
b. An iterative solution of the relevant equation
c. Computation of no load speed of the motor
d. Computation of converter output voltage
a. The same as input ac voltage
b. The same as the drop across the armature inductance
c. The same as the armature back-EMF
d. The same as the drop across the armature resistance
a. Forward motoring
b. Forward regenerative braking
c. Forward dynamic braking
d. Forward plugging
a. Duty interval
b. Coasting interval
c. Freewheeling interval
d. Zero-current interval
a. $75^o$
b. $65^o$
c. $30^o$
d. $15^o$
a. 861.2 rpm
b. 746.5 rpm
c. 505.9 rpm
d. 454.7 rpm
a. One
b. Two
c. Three
d. Four
a. Duty Interval
b. Coasting Interval
c. Freewheeling Interval
d. Zero-Current Interval
a. 960 rpm
b. 1029 rpm
c. 1423 rpm
d. 1561 rpm
a. 960 rpm
b. 1051 rpm
c. 1352 rpm
d. 1529 rpm
a. The converter operates in continuous current operation for speed greater than 720 rpm
b. The converter operates in continuous current operation for speed less than 720 rpm
c. The converter operates in continuous current operation for speed greater than 360 rpm
d. The converter operates in continuous current operation for speed less than 360 rpm
a. $f$
b. $2 f$
c. $3 f$
d. $6 f$
a. 231. 1 V
b. 305.6 V
c. 381.9 V
d. 421.7 V
a. By adjusting the triggering angle $\alpha$ only.
b. By adjusting the triggering angle $\alpha$ followed by armature connection reversal.
c. By operating with triggering angle $\alpha \gt 90^o$.
d. By connecting a freewheeling diode across the armature in addition to adjusting the triggering angle $\alpha$.
a. 1 & 2
b. 2 & 3
c. 3 & 4
d. 4 & 1
a. 0.54
b. 0.44
c. 0.34
d. 0.24
a. 0.29
b. 0.39
c. 0.49
d. 0.59
a. Duty interval
b. Freewheeling interval
c. Coasting interval
d. Energy storage interval
a. 0.023
b. 0.034
c. 0.066
d. 0.072
a. No conductors
b. Open circuited conductors
c. Short circuited conductors
d. A solid iron core
a. 1
b. 1.05
c. 1.13
d. 1.19
a. 0.75
b. 0.86
c. 0.95
d. 1
a. quite significant and it adds to the fundamental torque
b. quite significant and it subtracts from the fundamental torque
c. quite insignificant
d. pulsating in nature
a. a value close to half the synchronous speed
b. a value close to the synchronous speed
c. a value close to one fourth of the synchronous speed
d. a value close to zero
\(R_s = 1.5 \Omega\) , \(R'_r = 0.4 \Omega\) , \(X_s = X'_r = 1.2 \Omega\) , \(Xm = 50 \Omega\)
The peak value of the motoring torque, \(T{max}\), of the motor is
a.142.4 N.m
b. 165.3 N.m
c. 172.5 N.m
d. 192.3 N.m
a. It results in reduced torque and reduced power
b. It results in reduced torque but rated power
c. It results in rated torque but reduced power
d. It results in zero torque and zero power
a. 0.04
b. 0.96
c. 1.04
d. 1.96
a. Synchronous speed should be a little higher than the rotor speed
b. Synchronous speed should be a little lower than the rotor speed
c. Synchronous speed should be doubled
d. Synchronous speed should be increased by a factor of 1.5
$I_s^{1st} = 10 A $ , $ I_s^{5th} = 3 A $ , $ I_s^{7th} = 1.5 A $
Harmonics higher than 7th harmonic can be neglected. The rms value of the total stator current is
a. 10A
b. 10.31 A
c. 10.54 A
d. 14.5 A
a. Increase of synchronous speed
b. Decrease of synchronous speed
c. Reversal of the phase sequence of the stator
d. Increase of the stator voltage magnitude
a. 1,2,3,4,5,..
b. 1,5,7,11,13,..
c. 1,3,5,7,9,..
d. 2,4,6,8,10...